The 5 Ws of reshoring supply chains

This story is part of a Supply Chain Dive series on reshoring supply chains.
The calls are loud from industries, associations and the public sector: Bring supply chains home.
"Reshoring" spiked in Google search terms in early April, as shortages of critical medical supplies reflected the dangers of relying on foreign or single sourcing, particularly China.
U.S. National Economic Council Director Larry Kudlow encouraged U.S. companies overseas to reshore, telling Fox Business, "We will do what we can for full expensing and pay the cost of moving if they return their supply chains and their production to the United States." The U.S. government has put no formal policy in place to compensate supply chains for reshoring.
And former VP and presidential candidate Joe Biden released a plan last week to "rebuild U.S. domestic manufacturing capacity" if elected.
"Reshoring" spiked in Google search terms in early April
Google Search interest over time in the U.S.
Reshoring is not a decision supply chain managers can make in a vacuum. Does moving production or prioritizing local suppliers make sense in the larger context of the business? A variety of factors come into play, from customer desire to risk mitigation to total landed cost.
Supply chain managers have considered these elements since long before the coronavirus pandemic, and many started to transition toward reshoring as China's wages increased and tariffs took effect, Mark Hermans, managing director at PwC, told Supply Chain Dive. "[COVID-19] in some ways has acted as more of a catalyst."
What's reshoring, what's nearshoring and where are supply chains going?
Reshoring is the process of bringing manufacturing and part or all of the supply chain back to the home country from a foreign country. Nearshoring is a similar process, but refers to a location near the home country. In the case of U.S. businesses, nearshoring most often means sourcing from or manufacturing in Mexico.
In some cases, a firm will reshore its entire operation and supply chain, from raw material to finished product. "Nothing has to be global by nature," said Lisa Morales-Hellebo, co-founder and general partner at Refashiond Ventures and co-founder of The Worldwide Supply Chain Federation. She said the U.S. has the infrastructure and components to host full supply chains.
Your most critical supplies absolutely are being reshored. And rightfully so.
But more often due to labor costs, reshoring means bringing final assembly and perhaps the tier-one supplier to the U.S., but tier two, three and beyond may still be foreign.
Simone Ross, COO of supply chain management software company Setlog, gave the example of apparel companies that found tier one suppliers outside of China, mostly in southeast Asian countries. Nations such as Bangladesh do not have large swaths of raw material resources and continue to rely on China for those imports. So even though tier one moved, tier two remained in China. "We're still stuck to the country," Ross told Supply Chain Dive.
Hermans said most companies are considering or already using a hybrid model for their supply chains. A portion of production and suppliers may remain in Asia, while another part of production and some vendors are in Mexico and others in the U.S. "The combination gives you the flexibility to balance production based on customer needs," he said.
John Beattie, principal consultant at Sungard Availability Services, a disaster recovery and business continuity firm, said some organizations describe their sourcing strategy as "within market"— developing suppliers and standing up production geographically close to the customer.
"If your largest consumer base is not the U.S., put it where it is," Morales-Hellebo said. "If it's South Africa, build it up."
Local suppliers allow businesses to come closer to their partners, Ross said. "Deep collaboration is helpful in times of crisis."
Who's reshoring, and who's not?
Reshoring indices indicate the trend began to pick up last year.
Kearney's reshoring index found a 98 basis point increase in manufacturing import ratio for 2019. The Coalition for a Prosperous America's reshoring index reached 59 last year, indicating growth in U.S. manufacturing output and the largest positive move since 2002 (except for the recession year 2009).
The Reshoring Initiative lists more than 1,800 companies that have reshoredparts of their operations as of Jan. 1, 2019, including 3M, Apple, Dillard's, GM, KitchenAid, Oracle, Pfizer and Stanley Black & Decker.
Reshoring sees largest positive moves since 2009
CPA's reshoring index, measuring annual change in the share of U.S. consumption of manufactured goods that is met by US producers
And going forward in light of COVID-19 risks, 64% of 879 North American manufacturing and industrial professionals said they were "likely to bring manufacturing production and sourcing back to North America," in a Thomas survey.
Experts anticipate critical supply chains, such as those for healthcare products and personal protective equipment (PPE), will begin to reshore operations and prioritize resilience and stock over cost. "Your most critical supplies absolutely are being reshored," Morales-Hellebo said. "And rightfully so."
Bulky, industrial products such as automotive parts are attractive to nearshore, Hermans said, in part because of freight costs and lead times. Supply chains will also reshore if "Made in America" is important to brand image and their customers.
But not all supply chains will reshore or make significant supply chain changes post-pandemic. A June 8 Deloitte poll asked private companies to what extent they are considering reshoring and localization due to the impact of COVID-19. Of more than 1,300 respondents, only 6% made or plan to make significant sourcing or manufacturing changes. Sixteen percent made no changes.
Few businesses plan significant sourcing, manufacturing changes
% of respondents in a Deloitte poll to the question: To what extent are you considering more reshoring and localization due to the impact of COVID-19?
DHL customers have not been vocal about reshoring or nearshoring. "I'm hearing it in the news more than I'm hearing it from our customers today," Jim Monkmeyer, president of transportation at DHL Supply Chain North America, told reporters on a call in late May.
Industries such as apparel are likely to adopt a "China +1" strategy with other countries in Asia rather than moving to North America, according to Hermans.
Why would a business reshore or nearshore?
The decision to reshore is a balance between price and risk, according to Beattie.
Businesses need to examine the total landed cost, Ross said. Parts of that calculus include materials, manufacturing costs, labor wages, logistics and transportation, SG&A and tariffs.
A PwC analysis sent to Supply Chain Dive showed U.S. manufacturers who shifted production from China to Mexico could save 23% of their operating costs on average. PwC lays out a hypothetical example of an industrial product made in China with a total cost of $1,000. By moving production to Mexico, manufacturing costs per $1,000 product decrease by $17, logistics costs go down by $18 and tariff costs estimated at $182 in China are eliminated. The total cost of the product, therefore, becomes $771.
Manufacturing overhead is lower in Mexico, as wages have been steadily rising in China with the emergence of a middle class. China's labor costs surpassed Mexico's five years ago, according to PwC. "It's a nice balance of being able to achieve lower product cost as well as being closer to the market," Hermans said of manufacturing in Mexico.
Wages could rise with the U.S.-Mexico-Canada Agreement (USMCA) in place, though. The trade agreement includes an annex on collective bargaining rights for Mexican workers, which the U.S. said will "promote better working conditions and higher wages for Mexican workers."
China labor costs outpace Mexico's
Average compensation for manufacturing workers in U.S. dollars per hour
Other questions to consider in the reshoring decision, Hermans said, is the availability of an existing supply base, raw materials and skilled labor. And, perhaps most importantly, how much of an investment a business would have to make to move its production. Other factors could line up, but the investment "hurdle can still be too large to overcome," Hermans said.
COVID-19 put the spotlight on risk, as supply disruptions in China reverberated globally. But experts cautioned that local suppliers do not inherently eliminate risk. "More nearshoring does not necessarily mean that the supply chain is more resilient," Hermans said. "It's still a single point of failure."
Instead, resilience comes from diversifying vendor bases — a strategy more than one-third of professionals plan to deploy, according to a Procurious survey of more than 600 procurement and supply chain leaders conducted between April 28 and May 12.
And diversification can go hand-in-hand with nearshoring. A Michigan State University and Maine Pointe white paper recommend managers rebalance their offshore, nearshore and onshore mix for optimal operations.
When will supply chains reshore?
Reshoring is a long game. The decision-making process does not happen overnight, nor does the movement of a supply chain. The length of time to reshore also depends on how much of a supply chain is moving — whether it's the final assembly point or several tiers of suppliers.
Nearshoring efforts are ongoing for supply chains that made the decision during the U.S.-China trade war as tariffs shot up total costs, or before as China wages began to rise.
More nearshoring does not necessarily mean that the supply chain is more resilient. It's still a single point of failure.
But for firms that hadn't considered nearshoring before COVID-19 disruptions came into the picture, it may be too soon to decide on long-term changes that could require large-scale investment, according to Deloitte poll results. Nearly one-third of Deloitte survey respondents named a "high degree of future uncertainty" as their biggest hindrance to investing in supply chain resilience. About one in five respondents in the June 8 poll said they have not yet made a decision on reshoring and localization.
Instead, reshoring and nearshoring will start to gain momentum about six months after supply chains enter the "new normal," according to an AlixPartners report emailed to Supply Chain Dive. The trend will continue long term, until costs begin to outweigh benefits, the report said.
Ultimately, firms will diversify suppliers and nearshore their supply chains if the price is right. Current conditions are favorable for nearshoring in terms of cost and resilience. Logistics and labor costs are lower in Mexico than China, and suppliers closer to home reduce lead times and the risk of opacity in complex global supply chains.
"We're not going to see globalization entirely disappear," Morales-Hellebo said. "But it will prove to be less cost effective."
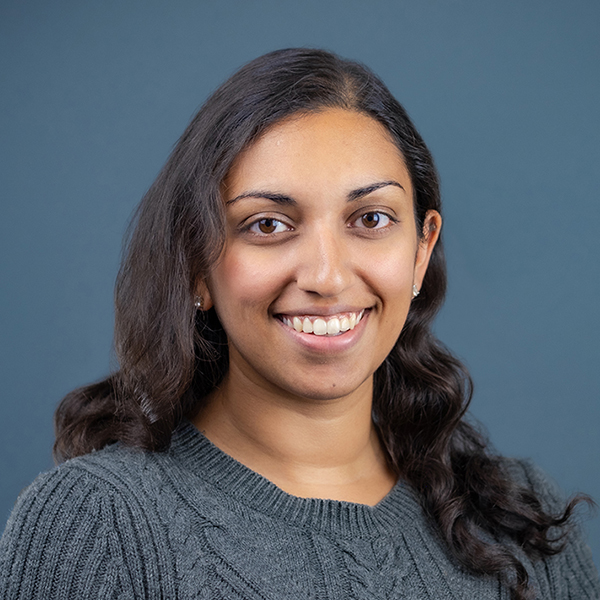