Impacts from the tragic collapse of the Francis Scott Key Bridge near the Port of Baltimore continue to send ripple effects throughout the supply chain.
A limited access channel to the Port of Baltimore is set to open by the end of April, with plans to fully reopen the channel by the end of May, but in the meantime, logistics managers must navigate continued disruption.
The challenges associated with the bridge collapse are two-fold, Lars Jokumsen, senior director of ocean product at Geodis Americas, told Supply Chain Dive in an email. The first challenge is for shippers with containers onboard the ship Dali, while the other is for shippers who had shipments booked or en route to the Port of Baltimore.
For shippers with containers onboard the Dali, the primary concern is if they could be on the financial hook for expenses related to the emergency, Jokumsen said.
“The challenges are more of a legal matter and whether or not the carrier will call “general average,” which is a maritime law that forces shippers to partake in the financial expenses in an emergency such as this,” he said. “With that, carriers will certainly help divert the cargo, but the associated costs fall on the shipper,” similar to what happened in 2021 when the Ever Given obstructed the Suez Canal.
On the other hand, shippers with cargo routed to the Port of Baltimore are now facing the issue of quickly sourcing short-term port and transport alternatives, Jokumsen explained.
Supply Chain Dive spoke to four freight forwarders to ask how they are traversing disruptions and delays at the Port of Baltimore, and what advice they are giving their shipper customers.
Navigating the delays
Forwarders are exploring alternative ports and transport modes — including air cargo for clients with time-sensitive shipments, Jokumsen said.
As the fallen bridge continues to block ship traffic, cargo destined for Baltimore will be diverted to ports the steamship line deems best, said Matt Castle, VP of global forwarding at C.H. Robinson. He added that this could be ports in New York and New Jersey or Norfolk, Virginia.
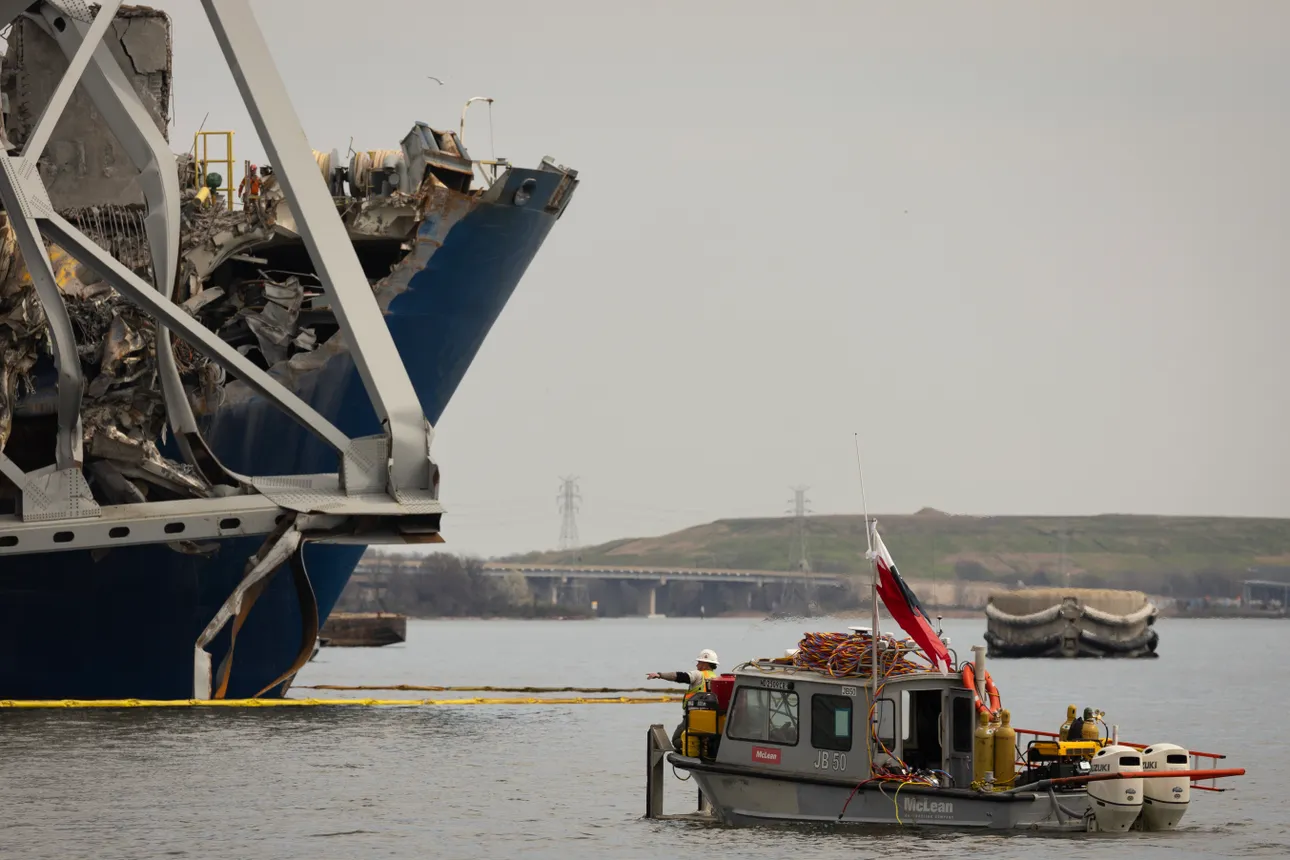
“We’re already making alternative plans to pick up those containers and arrange for truck or rail transportation from the new ports,” he explained. “For shipments that haven’t departed yet, we’re helping customers retrieve those containers from the Port of Baltimore and get them on their way.”
Ceva Logistics, meanwhile, is working closely with its ocean carrier partners to maintain cargo visibility and manage possible supply chain disruption, Joshua Bowen, global air and ocean leader at the company, told Supply Chain Dive in an email. Most carriers have already implemented contingency plans, and in the meantime, Ceva will monitor possible volume surges, congestion and equipment availability.
He added that there should be minimal delays for trucks coming into the port from the north. Meanwhile, trucks coming from the south need to take the I-05 or I-895 tunnels or navigate around the harbor to get closer to the Baltimore metro area.
Collaboration can help traverse short-term challenges
AIT Worldwide Logistics noted that it doesn’t anticipate significant challenges as a result of port diversions.
However, that doesn’t mean that cargo diversions won’t have ripple effects.
“One potential issue that could develop over the coming weeks relates to chassis deployment,” an AIT spokesperson told Supply Chain Dive in an email. “If a container is discharged at another port, but delivered on a chassis to the Baltimore area, in many cases, that chassis would need to be returned to the original port location, likely adding cost and emissions from deadhead miles.”
Jokumsen identified rail, terminal and draymen congestion as potential short-term challenges.
But there are ways to help traverse these challenges.
“My advice to shippers is to be as up-to-date and transparent as possible when communicating with your freight forwarder, especially when it comes to strategic adjustments and shifting requirements.”

Ryan Carter
EVP of the Americas at AIT Worldwide Logistics
AIT underscored the importance of real-time collaboration when it comes to transportation planning, which can help reduce the impact of supply chain disruptions, according to Ryan Carter, EVP of the Americas.
While AIT is keeping an open line of communication with customers about alternative shipping lanes or transport modes, the spokesperson added that the forwarder is also using real-time visibility technology to “help customers stay on top of the situation.”
“Part of the role of an effective logistics service provider is to continually re-evaluate the physical connections in the supply chain for customers, including warehouses, roadways, airports and seaports,” Carter said. “My advice to shippers is to be as up-to-date and transparent as possible when communicating with your freight forwarder, especially when it comes to strategic adjustments and shifting requirements.”
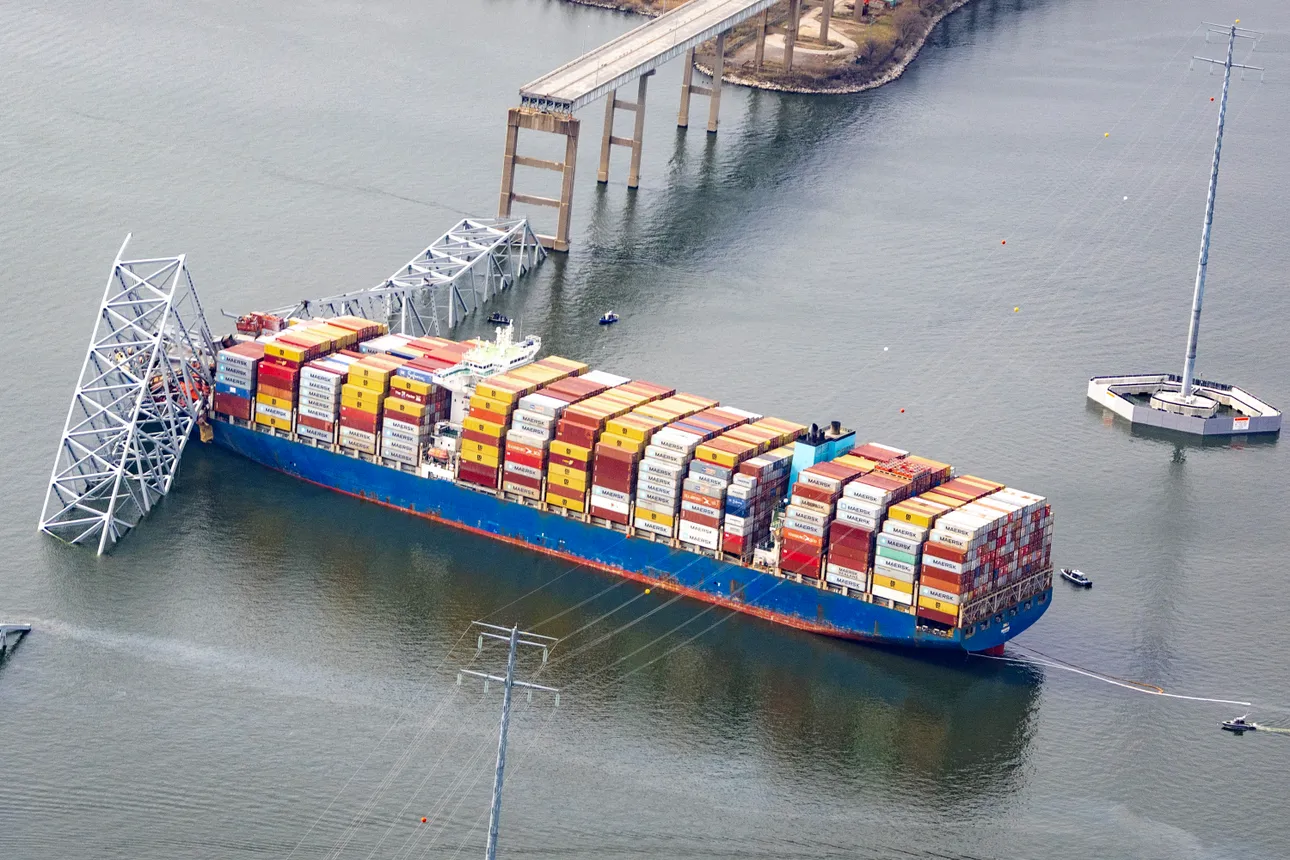
Surrounding ports are capable of handling the diverted container volumes due to solid rail connectivity and other modes of transport, Jokumsen said.
“The immediate area of focus is securing the capacity needed to allow containers to move from depots, container yards, etc. where there is a risk of accruing per diems,” Jokumsen added. “We continue to keep a close eye on the containers we are directly managing to avoid any unnecessary storage, and we are passing the same advice on to customers where we are not directly involved.”