Kali Bonnell has built her construction career at Redwood City, California-based DPR Construction, where she worked her way up from intern in 2008. In May, she advanced from project engineer with the firm’s Special Services Group to its Atlanta business unit leader.
Atlanta’s market is a diverse and unique one, according to Bonnell, which allows the company to tap into all of its core markets, including advanced technology, commercial, healthcare, higher education and life sciences. In her new role, she’s excited to collaborate with clients, design teams and trade partners to bring a shared vision to life.
Here, Bonnell talks about navigating supply chain pressures, DPR’s green building efforts and the stories her grandfather told her that drew her to construction.
This interview has been edited for brevity and clarity.
CONSTRUCTION DIVE: What are some of the biggest challenges the industry is facing right now?
KALI BONNELL: We continue to manage through the skilled labor shortage as well as increased costs and supply chain pressures which are common across the industry. In terms of the supply chain, we are experiencing very long lead times for generators, transformers, certain types of wiring and stainless steel tubing.
Yet, we are seeing a ton of positive indicators in the marketplace: Construction employment is at an all-time high, inflation is decreasing month over month and growth is anticipated over the next 12 to 24 months with a very strong pipeline into 2026.
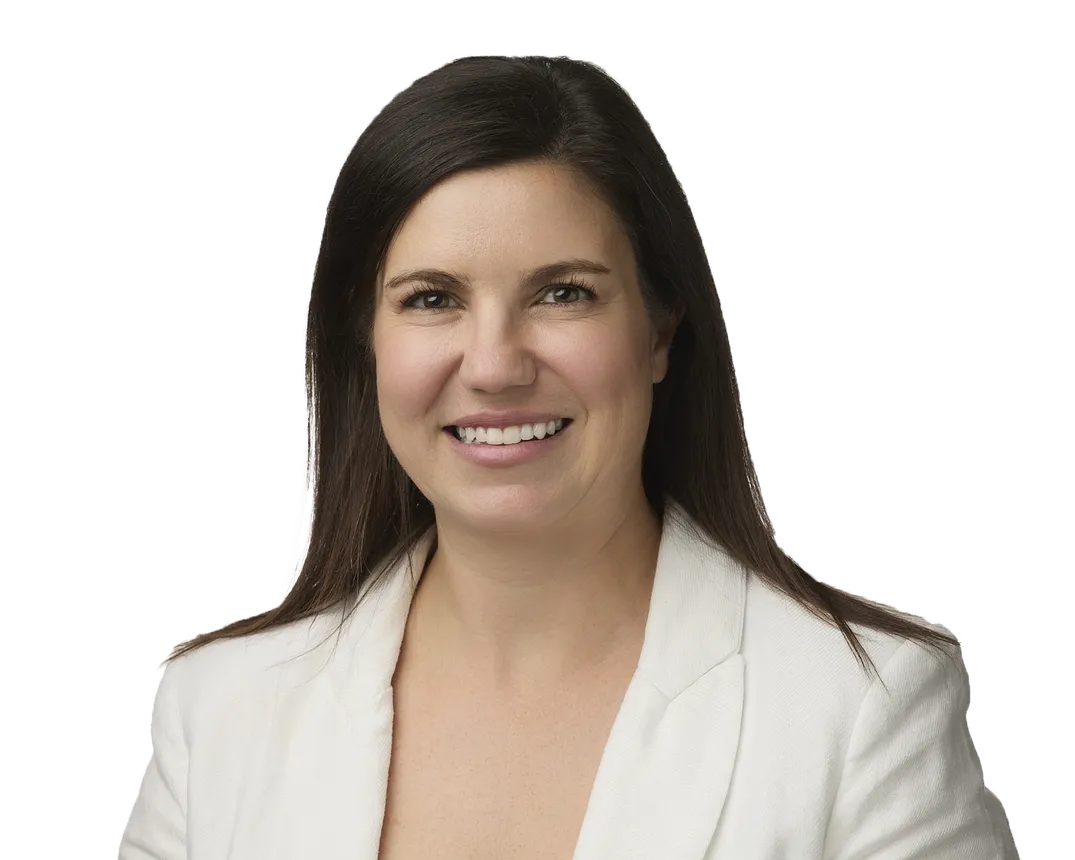
Our approach to mitigate impact is long-term strategic planning, developing relationships with manufacturers and putting a logistics model in place that allows for early ordering and flexible storage close to jobsites. We will continue to see long lead times, although many areas have improved and started to settle.
It’s more important than ever to plan well and early by collaborating across disciplines and bringing your team to the table early — that’s where we can have the most impact on costs and delivery.
How is DPR Construction incorporating climate-friendly building strategies?
DPR first aligned with the U.S. Green Building Council in 1998. Walking the talk is in our DNA which is why sustainable practices are a key part of our approach to global social responsibility.
Here in Atlanta, we are working on several LEED and WELL Building Standard projects. We have a project in Norcross, Georgia, that is working toward LEED-Platinum. It includes an irrigation reuse cistern, a stormwater detention vault designed to capture runoff, a photovoltaic system to harness the sun's energy and a geothermal system to reduce the campus' energy load.
Many of our other projects in Atlanta are tracking LEED standards and we have focused on waste diversion from landfill ranging between 85% and 96%. Our projects incorporate water hydration stations reducing dependence on single-use plastics.
We constantly pursue ways to make our jobsite operations more sustainable through waste reduction, innovative technologies and efficient jobsite offices and ensure that every project controls environmental aspects that affect the surrounding community. Our new office space in Atlanta is incorporating sustainable components and is tracking for WELL certification.
What drew you to construction? How can the industry attract more women?
I have always been enamored with construction. I love seeing things come to life in real-time. My grandfather was an electrician and would tell me stories of the high-rises he helped build in Philadelphia when I was a child. I began my career in Atlanta in 2009 upon graduation from Auburn’s Building Science Program and since then have had the incredible opportunity to see many buildings come to life throughout the Southeast.
There are more women working in construction than I think people may be aware of. For me — and here at DPR in general — fostering an inclusive environment is a priority each and every day. This includes everything from the language we use to the safety equipment we wear.
Early in my career I would have a hard time finding PPE that fit properly. Our culture brings the conversation to the forefront and acts on them — for example, one of our project managers worked with PPE manufacturers to create a vest solution for all.
DPR is also an organizer and ongoing supporter of Construction Inclusion Week, which aims to build awareness of the need to improve diversity and inclusion in the construction industry.
Can you tell us about your favorite project? What did you learn?
I love technical builds, particularly within healthcare where we often must contend with a worked-in environment and ensure we do not disrupt patient care. One such project was a complex, two-floor vertical expansion of an existing Florida hospital that heavily utilized prefabricated components to make the project as smooth as possible.
Prefabrication was relatively new for me at the time, and it was an eye-opening experience to see the efficiency that can be gained with offsite construction. We were able to reduce the impact to the hospital staff and patients by reducing our schedule. I also saw first-hand the opportunities to improve project quality and safety with offsite construction by eliminating high-hazard activity.