The following article is part of a weekly series, where Supply Chain Dive asks five industry influencers to comment on a recent news item, trend or skill set. To read more about the participants, please click here.
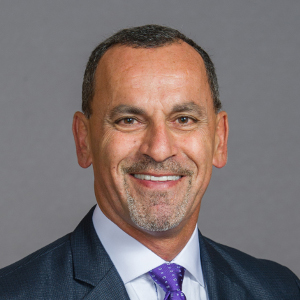
Abe Eshkenazi
CEO, APICS
The trend of reshoring production is rising amongst domestic manufacturers, but supply chain, logistics and operations management professionals still must assess those decisions from every angle. Beyond considering cost of labor, other factors include ease of outsourcing, effectiveness of supply chains and whether innovation is more likely when research and development and manufacturing occupy the same space. Offshoring has potential benefits: closer access to raw materials, specific technical expertise and potentially lower labor costs. However, these strategies tend to increase supply chain complexity and bring on greater risks, such as on time delivery issues, failure of technology systems or electrical grids, or delays related to weather occurrences.
To make well-informed decisions around offshoring, nearshoring, or even reshoring, supply chain managers should hone their critical thinking skills and continuously equip themselves with the most up-to-date and trusted industry insight. This means studying proven practices, understanding emerging drivers in supply chain and making a commitment to never stop learning.

Cathy Morrow Roberson
Founder and Head Analyst, Logistics Trends & Insights
For many companies, lower labor costs and proximity to raw materials have been the main reasons for offshoring. However, global political winds have resulted in a rethink. The US, for example, recently pulled out of the Trans-Pacific Partnership and NAFTA is now in jeopardy of being disbanded. Meanwhile, the UK’s vote to leave the EU has created more questions than answers for businesses operating in the UK. The uncertainty has resulted in some international businesses to consider relocating to continental Europe as a result.
However, despite such moves, offshoring remains alive. China, long known as the world’s manufacturer, is shifting towards a balanced economy that of equal exports and imports. As a result, it has offshored lower labor cost manufacturing to other Asian countries and created an intricate spider-web like regional supply chain. Similar situations exist in Europe and elsewhere.
As such, the future of offshoring/nearshoring can very well be these types of regionalized supply chains.
In terms of preparing for potential disruptions, having a plan to mitigate is necessary. The plan should provide such details as alternative manufacturing locations, suppliers, when to change mode of transport, port and airport alternatives and so on. Also, end-to-end visibility into one’s supply chain is vital. This allows managers to know not only the status of goods but where they physically are. Additionally, it will help validate all the manager’s suppliers and not just the tier one suppliers. Lastly, regular communication and collaboration with all supply chain partners is also helpful towards mitigating potential disruptions.

Jon Slangerup
President and CEO, American Global Logistics
In my view, there are a few angles to look at when discussing nearshoring and offshoring as being disruptive to managing or optimizing supply chains.
First of all, the practice of nearshoring and offshoring (N&O) is hardly something new. Businesses have been pursuing lower labor costs for decades, without sacrificing quality. Therefore, any ‘disruption’ from a labor perspective is already a common business practice, and the adjustments to supply chain management is fully engaged on a global scale.
N&O responds naturally to changes and shifts in global manufacturing, based on location, cost and quality. If you can source a product for less without sacrificing quality or speed to market, then the closer or more accessible the source is, the better. From a U.S. perspective, this has played out with the strong consumer demand for low-cost goods produced offshore in Asia. However, you only have to look to Canada and Mexico to see the tremendous impact that “nearshoring” has had on North American trade and jobs.
However, I think the more relevant and compelling conversation focuses on the impact of automation on reducing labor costs and the related opportunities for “reshoring” and optimizing supply chains. Artificial intelligence and robotics (AI&R) are rapidly transforming the face of global manufacturing and operations, which will ultimately enable goods to be made at or near the point of consumption. At the same time, the processing, handling and delivery of goods (multi-modal logistics, warehousing, driverless trucks and drones, etc.) will further optimize workflow.
As it has done since the beginning of history, commerce will follow the least path of resistance to fulfilling demand for goods and services. While N&O is the common practice today, AI&R is the next highly disruptive wave that governments, businesses and individuals need to prepare for.
