Editor’s note: This story is part of a series on the tactics healthcare executives are using to address supply chain challenges. Read the previous installment here.
The Memorial Sloan Kettering Cancer Center used to have a fragmented supply chain. Although the hospital system employed a corporate purchasing team, it only processed purchase orders and requisitions from the various sites, and each MSKCC location had the authority to sign contracts on its own, within its given approval levels.
In 2018, Kreg Koford was brought on as SVP of supply chain and hospital operations to change that.
“We started a major transformation to design what a modern supply chain would look like,” he said. When COVID-19 hit in early 2020, “we were able to leverage the pandemic as an accelerant to our organizational change to bring end-to-end control of the supply chain.”
Koford’s department is responsible for the network’s entire supply chain, which includes $1 billion in non-labor expenses, such as purchased goods ranging from hospital equipment to bedside supplies, and services like nutrition.
Although MSKCC has just one hospital, it runs three ambulatory care sites in New Jersey and 15 clinical care and administrative sites in New York state, with a dozen of those located in New York City, according to the hospital group’s website.
How central reporting and purchases streamlined operations
Koford’s team is consolidating all purchasing processes and developing an overarching procurement policy. The policy change will be institution-wide, shaping which teams are responsible for making and authorizing transactions based on dollar thresholds and risk levels to MSKCC.
The hospital also integrated its supply chain with its ambulatory care facilities to create a centralized organizational structure across all sites. This required building coalitions with the ambulatory sites to gain their trust, and has helped the healthcare institution standardize sourcing, ordering and replenishment at a faster pace.
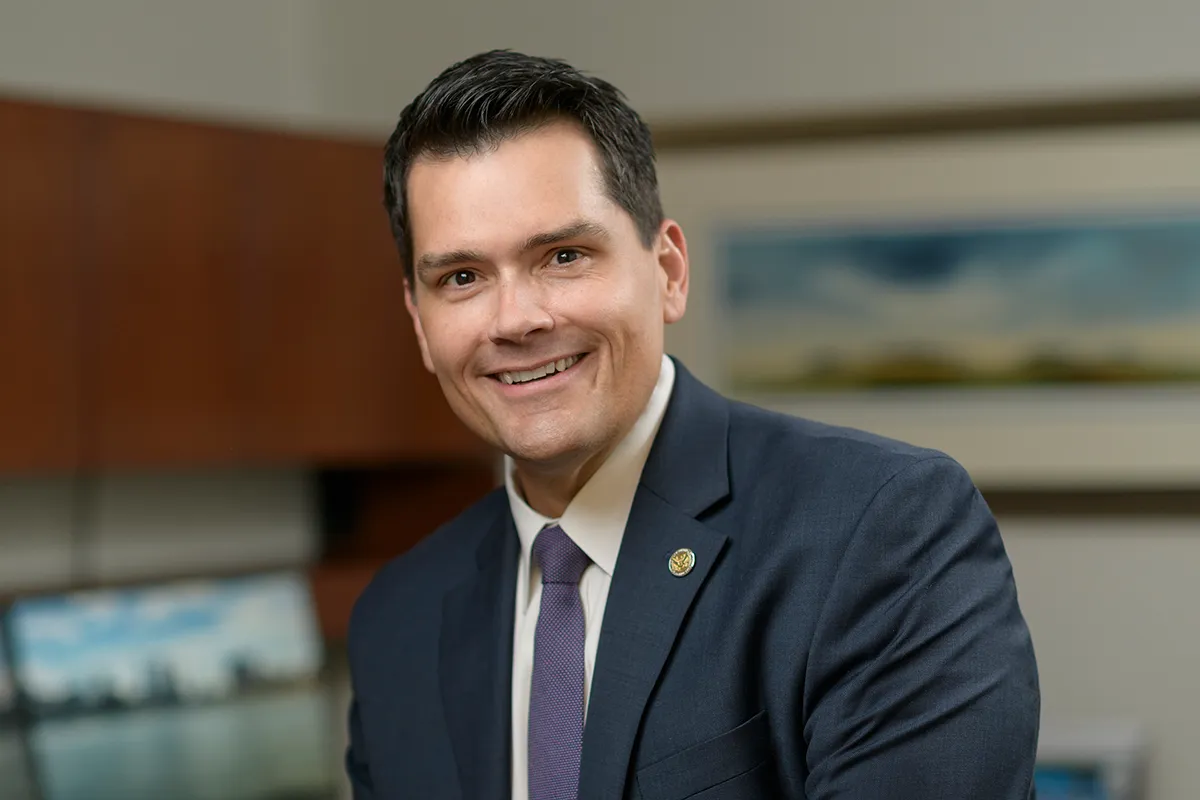
“Backorders were also managed independently by each site, so we developed a centralized backorder management program which helped address network wide shortages and eliminate competition among our locations,” Koford said.
Working with the materials management leadership, Koford created a comprehensive plan to support individual sites and the enterprise level of the supply chain. That included identifying which resources would benefit from central reporting versus individual site reporting and building a corresponding plan.
To provide MSKCC with workflow visibility, the team identified the necessary resources, workflows, technical and training opportunities needed, including insights into what the organizational structure should look like. They implemented standardized receiving policies and procedures, along with materials management audits and regulatory readiness processes, to handle things like expired items and infection control.
Materials management teams are still responsible for receiving and storing their products, but they now share technology, processes and reporting methods, Koford said. Supply chain staff roles across the organization were also standardized to help with understanding responsibilities, training and career path planning.
Using data to improve the supply chain
Koford is leveraging tech solutions to increase the department’s use of data for forecasting, inventory management and supply strategies, which is managed by a single team.
Koford’s department added a hub-and-spokes model to improve distribution control, aligning inventory with forecasted needs. The data dashboards are integrated into MSKCC systems, so all sites can access them for informed decision-making. That forecasting was particularly helpful because the pandemic forced MSKCC to abandon just-in-time replenishment.
Koford’s team also created a digital twin for its inventory and procure-to-pay system so they can analyze data on contract utilization, supplier consolidation and SKU optimization, to extract additional savings.
Building supply chain resiliency
Following supply chain uncertainty spurred by the pandemic, MSKCC is thinking beyond its walls to ensure resiliency. That includes considering potential global and domestic disruptions, such as natural disasters. Koford’s teams are currently working with an emergency planning group to track local disruptions.
MSKCC’s materials management team is helping lead those efforts, which include working with manufacturers and distributors to understand their risk mitigation plans.
The health system also rethought its warehousing efforts during the pandemic, after finding out it lacked the capacity to store state-mandated levels of personal protective equipment.
MSKCC initially worked with its distributor to store pandemic inventory, but it has since shifted to using its warehouse as a strategic asset to hold safety stock of critical items.
“We can place bulk purchases and carry inventory to help manage through supply disruptions in the market much more effectively,” Koford said.
MSKCC is also interested in moving to a consolidated service center model, but it is difficult because costs in Manhattan are high.
“It’s something that we are considering more and more to make sure that we have more control upstream of our products, and the ability to meet demands under whatever circumstances.”