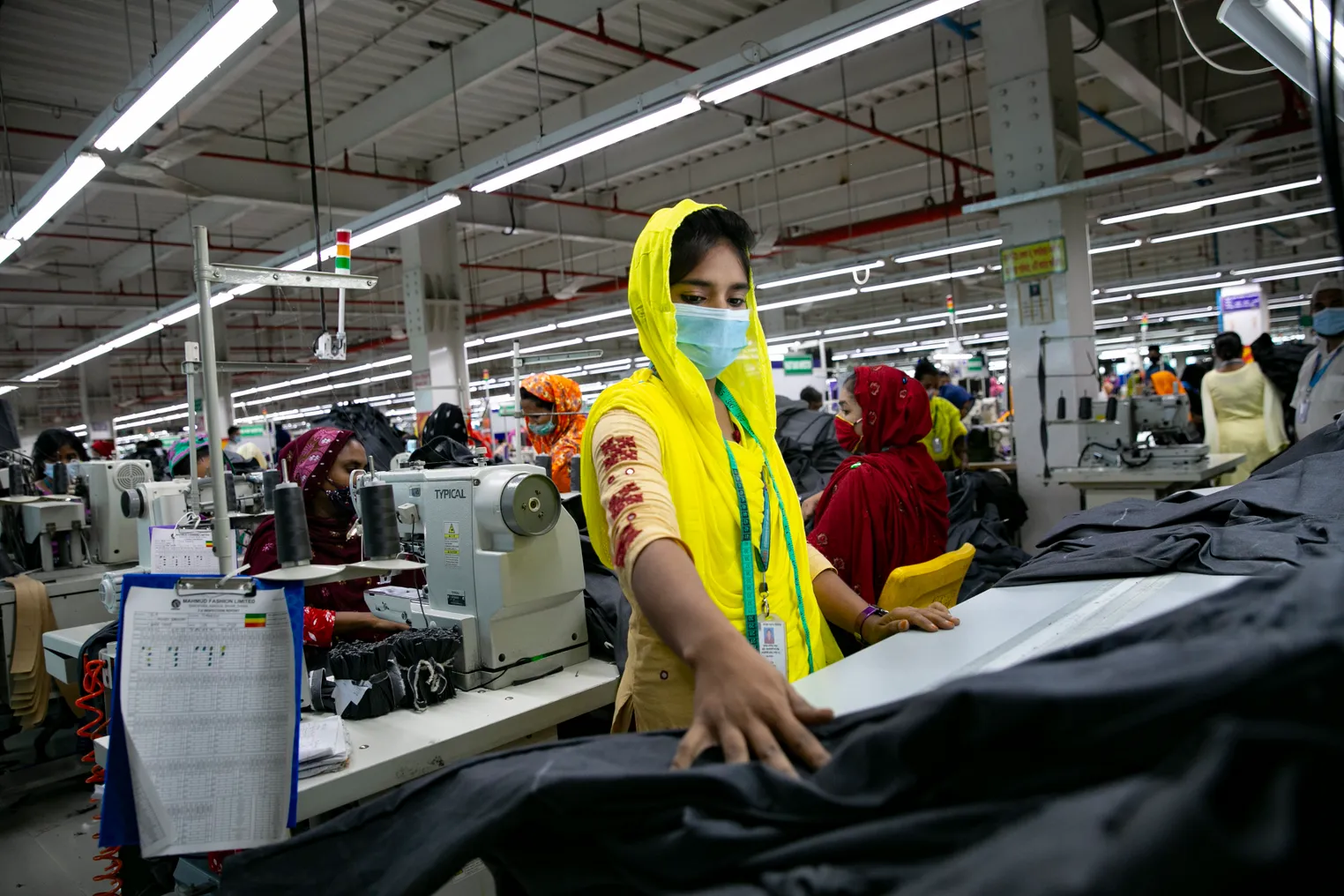
3 years later: How COVID-19 exposed the vulnerability of suppliers and workers to the power of big buyers
Three years ago at this time, thousands of retail doors across the U.S. were shuttered as COVID-19 began its rapid, deadly spread.
Factories in Bangladesh, Sri Lanka, Pakistan, Cambodia, Ethiopia and other global manufacturing hubs also shut their doors after large retailers and brands — facing deep uncertainty in their own businesses — canceled many billions of dollars’ worth of orders.
The two sets of closures are related, but the ultimate outcomes were vastly different and unequal.
Most retailers and brands in the U.S. shrugged off the financial impact of the store closures within a year. Meanwhile, many smaller factories closed for good, while workers were laid off and lost desperately needed income. Debt, forced labor and hunger followed the lost wages for many factory workers, especially in apparel and footwear, where incomes historically have been low to begin with.
The early period of the pandemic revealed the cracks in supply chains as well as the underlying dynamics that are still very present by many accounts, and which predated the crisis.
For all the talk of partnership between buyers and suppliers, the COVID-19 crisis showed just how contingent the relationship often is between powerful brands and overseas vendors and their workers, as research since that time has shown.
“It lays bare the vulnerability of the supply chain for the workers,” Pamela Abbott, a professor of education and director of the Centre for Global Development at the University of Aberdeen in Scotland, said in an interview.
‘They were just in shock’
Walmart. Target. Aldi. Kohl’s. Gap Inc. H&M. Inditex. VF Corp. Carter’s. J.C. Penney. Tesco. Those are just some of the companies that canceled orders with suppliers early in the pandemic crisis, according to academic researchers.
By late April of 2020, major brands had canceled $3.8 billion worth of apparel orders in Bangladesh alone, as Mark Anner, labor professor and director of the Center for Global Workers’ Rights at Penn State, found by using a database released at the time by a trade association of Bangladeshi manufacturers. And that was in just one country.
Some of the order cancellations were especially damaging financially. In many cases, suppliers had already spent capital to procure raw materials or had manufactured the products — some orders were even on boats in transit to their buyers.
“They were just in shock,” Anner said in an interview with Supply Chain Dive. “[Suppliers] were in debt, operating on credit, and getting paid later and later over time. … When you cancel on them, when they’re in debt to the banks and everyone else, the ripple effects are very severe.”
Force majeure — previously a boilerplate contract and legal term — took on new and dire meaning for suppliers. Literally meaning “a superior force,” buyers began invoking it to cancel orders en masse. Many suppliers were caught completely off guard. “‘Where is this clause?’” Anner said, describing supplier confusion at the time.
"When you cancel on them, when they’re in debt to the banks and everyone else, the ripple effects are very severe."

Mark Anner
Professor and Director of the Center for Global Workers’ Rights, Penn State
If the orders were already produced, suppliers were typically stuck with the goods. Garment factories in Bangladesh, for example, had to sell into local markets at much lower prices given that clothes for Western markets are very different from what people in those areas wear on a daily basis, as Muhammad Azizul Islam, chair in accounting and professor of sustainability accounting and transparency at the University of Aberdeen, noted in an interview.
And cancellations weren’t the only damaging actions by buyers. Brands also reduced new orders, delayed payments and started paying on longer terms as they tried to minimize their own risk. In effect, they shifted financial and operational risks to their suppliers, researchers and activists said.
About half of factories in a survey of Bangladeshi apparel producers reported that retailers engaged in at least one practice deemed unfair, whether it be order cancellation, price reduction, refusal to pay for dispatched goods and delayed payments, according to a paper from this January by Abbott, Islam and other University of Aberdeen researchers. Larger brands and retailers were more likely to engage in those practices compared to their smaller counterparts.
Debt, hunger and instability
Suppliers didn’t simply absorb all of the financial pain. As research has found, it moved further down the chain to workers. And many are still living with the ramifications today, three years later.
As store and factory doors shut, workers had their hours cut, or were furloughed or laid off.
The University of Aberdeen authors found that at least 25% of factory workers in Bangladesh lost their jobs during the March-April period in 2020, based on a survey with factory owners. The figure could be similar in other production areas around the globe.
Nearly 80% of garment workers who lost their pre-pandemic contracts had not received full severance pay, and more than two-thirds had received nothing, according to a 2021 report from University of Sheffield and Workers Rights Consortium researchers that surveyed over 1,110 workers.
Wage claims amounted to $24 million across 467 factories in six countries for Levi’s, Nike and VF Corp., according to a joint report from Asia Floor Wage Alliance and Global Labor Justice-International Labor Rights Forum.
That number covers only a small fraction of the supply chain. But if the average from that survey — $1.1 million in wage claims per factory — is any gauge, the unpaid pages owed to workers from the COVID-19 crisis would amount to many, many billions of dollars across the global supply chain just for the fashion industry.
The decimation of worker incomes had several consequences. Looking at workers in Ethiopia, Honduras, India and Myanmar, a team of researchers working with the WRC found that supply chain workers in the garment industry saw their living conditions worsen, as the few who had savings had to spend it to survive, and many more took on new debt. Along with borrowing costs, the nature of lending in many areas has made workers more vulnerable to forced labor and other abuses since 2020.
Workers also faced food insecurity and outright hunger. In a survey from November 2020, 88% of garment workers reported that their household had to reduce food consumption because of diminished income, and 77% said they or a family member had gone hungry at some point, according to a separate WRC study. Twenty percent of workers said they experienced hunger on a daily basis at the time.
“Workers weren’t very well off before COVID-19. COVID-19 just exacerbated pre-existing issues.”

Pamela Abbott
Professor and Director of the Centre for Global Development, University of Aberdeen
Returning to factories after economies reopened in the West didn’t resolve the difficulties for workers. Islam said that employers pushed new contracts on those who had been laid off, and workers were desperate enough to sign even at less pay.
“Whatever the employer offered, you had to accept it,” Islam said.
When sales in wealthy countries picked back up and brands tried to restock in a hurry, schedules became frenetic, and many workers reported unpaid overtime.
Accelerated production schedules put even more pressure on those workers who still had jobs after the initial crisis. Many since have reported unpaid overtime. Those overtime wages are critical, as many workers in poor countries rely on them to make ends meet.
"Intensified production targets and all types of wage and hour violations that the garment industry is kind of known for has been heightened over the past years, because of the instability in supply chains and suppliers trying to make up for their margins on the backs of workers," said Sahiba Gill, senior staff attorney with GLJ-ILRF.
None of these ills for workers were new to the pandemic. Below-cost purchasing, rapid timelines, and last-minute order changes by buyers have pressured factories and in turn their employees.
“Workers weren’t very well off before COVID-19,” Abbott said. “COVID-19 just exacerbated pre-existing issues.”
A ‘character moment’ for buyers
After the initial crisis, many brands began paying for canceled orders. Anner pointed out that this was in part due to public pressure on brands, as they were called out for their actions in public.
Workers and suppliers began collaborating on activism, including through what was dubbed #PayUp, a campaign to pressure buyers to pay for canceled orders during the crisis.
As Anner wrote in a 2022 paper, collaboration between workers and factory owners on activism happened as “suppliers realized that they needed the moral legitimacy of activists and worker rights advocates, and because worker rights advocates understood that if suppliers went out of business, millions of workers would lose their jobs.”
Much of the visibility to the issue has passed with the initial crisis. And the cases of brands financing lost severance remain extremely small in number. One of the very few is Victoria’s Secret, which came to a historic settlement with workers in Thailand in early 2022 over wages lost amid a 2021 factory closure.
Again, that’s the exception for now. At the end of 2022, 90% of factories studied by the Asia Floor Wage Alliance had not resolved workers’ wage claims going back to 2020, and more than half had not paid for owed overtime also tracing back to 2020.
And that is after years of activist pressure on the brands in the study. One of those brands, Nike, was recently the subject of a complaint by unions and activist groups with Organisation for Economic Co-operation and Development over treatment of workers in the sportswear giant’s supply chain, much of it tracing back to the early 2020 period.
“We're really hoping that they will find a way to pay back workers and their supply chain, and they can also change the way they do business moving forward.”

Sahiba Gill
Senior Staff Attorney, Global Labor Justice-International Labor Rights Forum
For Anner and others who study the relationships between buyers and suppliers in fashion and other markets, the crisis in 2020 highlighted just how unequal the partnership can be, and how workers in poorer countries ultimately absorb the brunt of buyers’ actions.
“Buyers squeezed suppliers on price, order volume and payment terms, with devastating consequences for suppliers and especially for workers,” Anner summed up in his 2022 paper. “Millions of workers lost wages, jobs and severance payments.”
The lasting impact is relational as well as material. “Partnerships and trust were severely damaged — between buyers and suppliers, and between factory owners and their workers,” Anner said in an interview. “That has to be rebuilt.”
It’s unclear what has changed in the relationship between large buyers and overseas suppliers. Among big brands, 72% were paying below the cost of production in late 2021, and 68% were buying from factories that were struggling to pay their workers the local minimum wage, according to the University of Aberdeen authors.
Some say the plight of workers in supply chains is just as precarious today, if not more so, and that buyers’ actions remain just as problematic.
“From what we've heard, I would say a lot of the buyers have not improved their relationships, and they've actually doubled down on some of their practices,” said one researcher who studies labor issues in supply chains.
For Abbott and Islam, the issues are systemic. As they explain, countries compete to be manufacturing hubs and attract foreign investment. Factories within those countries and in others all compete to win contracts. Buyers, facing investor pressure to generate profits, push down suppliers’ prices as far as they can. The rock-bottom prices and pressures on factories can lead to all manner of abuses against workers. And everyone in the system is competing to supply consumers vying for status and trying to keep up with cultural norms.
While the global supply chain crisis of 2021 showed just how much buyers rely on their suppliers, the following year saw buyers rolling back and canceling orders — albeit not with the same level of destructiveness as in early 2020 — once sales began to decline. But researchers Supply Chain Dive spoke with said workers are once again feeling the pain of buyers’ defensive actions.
"It is a real bellwether character moment for the industry, and they can still make good,” Gill said. “We're really hoping that they will find a way to pay back workers and their supply chain, and they can also change the way they do business moving forward.”